A composite nonwoven fabric comprises two layers of melt-extruded filaments, one upper and one lower. The two layers are superimposed on one another and are contiguous with the supporting layer 11. The outer facing layers have characteristics similar to textile fibers. The individual fibers are oriented in the widthwise direction of the fabric, thereby providing strength and stability. These qualities make the material desirable for many applications. The invention is directed towards improving the efficiency of textile manufacturing.
The outer ply 11 has a basis weight of three to thirty grams per square meter. It is made up of continuous multiconstituent filaments bonded together. The outer ply 13 is also a spunbonded nonwoven web of substantially continuous thermoplastic filaments. The composition and basis weight of the outer ply 13 are similar to those of the inner twelfth layered nonwoven.
The composite nonwoven fabric of the invention exhibits good strength-to-breathability balance, excellent barrier properties, and excellent stability to gamma rays. The fibers in the fibers are oriented lengthwise and bonded at crossing points. The supporting layer is covered by upper and lower three-dimensional self-sustaining facing layers. These layers are stitched together using row-stitching stitches that penetrate the two layers and connect the individual fibers of each layer.
The composite nonwoven fabric of the present invention exhibits excellent balance between strength and breathability, barrier properties, and gamma-radiation resistance. It is a superior alternative to current materials and is suitable for use in medical and industrial applications. Its Gurley air permeability is 35 cfm for fabrics with base weights ranging from 40 to 120 grams. These features make it a preferred material for a variety of applications.
A composite nonwoven fabric comprises three layers of fibers. The inner ply is sandwiched between the outer plies. The composite fabric has good strength, flexibility, and drape. It can be used in protective garments. It can also be made of waste cotton, which makes it more environmentally friendly. Its cost of production is lower than the standard nonwoven fabrics. Its elasticity and breathability make it a more attractive option for many users.
A composite nonwoven fabric comprises three layers of self-bonding fibers, preferably synthetic organic fibers, which extend in random directions throughout the layer. The fibers are bonded together at the cross-points where they overlap. The supporting layer has an upper and lower three-dimensional self-sustaining facing layer on the opposite sides. Both of these layers are stitched together by rows of stitches that penetrate the layers and stitch the individual fibres of the facing layers. In addition to its strength and breathability, the composite nonwoven fabric can have a ribbed or napped surface.
The composite nonwoven fabric is bonded together by discrete point bonds. Each component comprises one or more polyethylene microfibers. The composite nonwoven fabric can be used in a variety of applications. For example, it can be used in biomedical products, such as surgical gowns. It can also be made from cotton. It is biodegradable and can be recycled. There are no known side effects associated with the use of the composite nonwoven fabric.
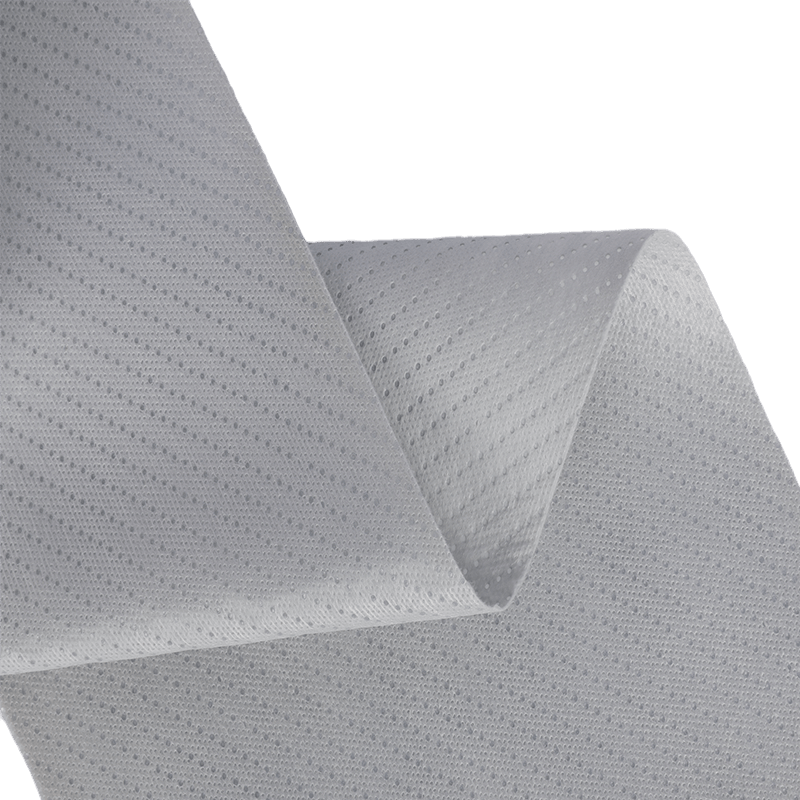
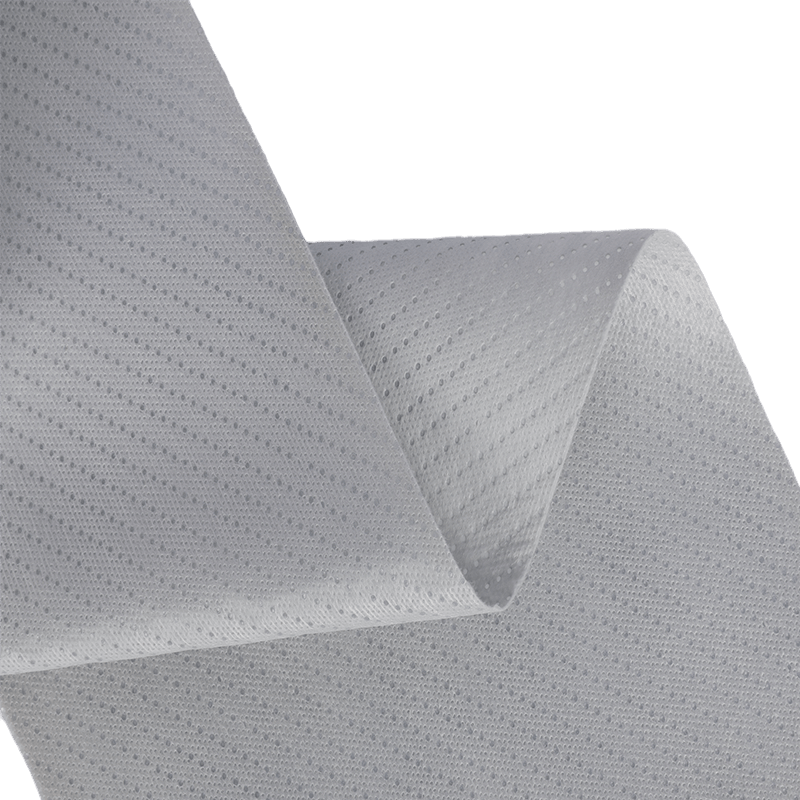