The composite nonwoven fabric of the present invention includes elongated rows of stitches 20 that penetrate the superimposed layers 11 and 14. These stitches stitch the individual fibers of the upper and lower facing layers together. The rows of stitches extend lengthwise throughout the fabric to provide strength in the lengthwise direction. The rows of stitches are used for multiple purposes, including a variety of protective garment applications. In one embodiment, these rows are bonded by a resin.
The chapter on nonwoven fabric covers a range of medical applications. It discusses applications of surgical gowns, clinical wearables, and swabs. Other topics include scaffolds for tissue engineering, hernia meshes, filtration materials, and incontinence products. Listed below are some of the most popular uses of nonwovens in medical applications. You can learn about the various uses of composite nonwovens in your daily life by reading the chapters in this book.
The basic composite nonwoven dressings of the present invention are commercially available and versatile. The surgical gown 95 is made from a composite nonwoven fabric with a hydrostatic head rating of 35 cm and a bacterial filtration efficiency of 85 percent or higher. The surgical gown 95 is fabricated by sewing precut panels together or by fusion bonding. In addition to this, the nonwoven absorbent layer includes medication that promotes healing.
The high strength and filtering capabilities of this composite nonwoven fabric have made it a preferred material for medical and industrial filtering. Its use in ventilation and bio engineering is growing. It helps to keep the environment clean by preventing particles from exchange with the outside world. It is also an excellent filter material for electrical components and pharmaceuticals. And because it is nontoxic, SMS has found a place in the industry for medical and industrial filter materials.
Thermal bonding is an important aspect of composite nonwoven fabrics. The process of fusion bonds two or more pieces of fabric together, with the lower melting component maintaining substantially continuous fibrous structure along the seam. This bonding is necessary to avoid pinholes in the fabric, which may compromise its barrier properties. In addition, thermal bonding may lead to a reduced level of inter-ply adhesion. If this is the case, the composite fabric may become unstable.
Another feature of the composite nonwoven fabric is that it can be used for electromagnetic interface shielding. The amount of carbon fiber in the fabric affects its EMI shielding effectiveness. Typically, the greater the carbon fiber content, the higher the EMI dominant mode. When compared to other materials used for shielding, composite nonwoven fabrics are superior. For this reason, they are often used in electromagnetic shielding. So, before using a nonwoven fabric for electromagnetic shielding, make sure you know how it works.
Fibers used in the manufacturing process of composite nonwoven fabrics can also be made from polyethylene terephthalate. The polyethylene terephthalate fibers, for instance, are widely used in nonwoven fabrics. This fiber also improves their abrasion resistance. The bonded fibers are disposed in a pattern shaped to enhance the ability of the nonwoven fabric to repel abrasive particles.
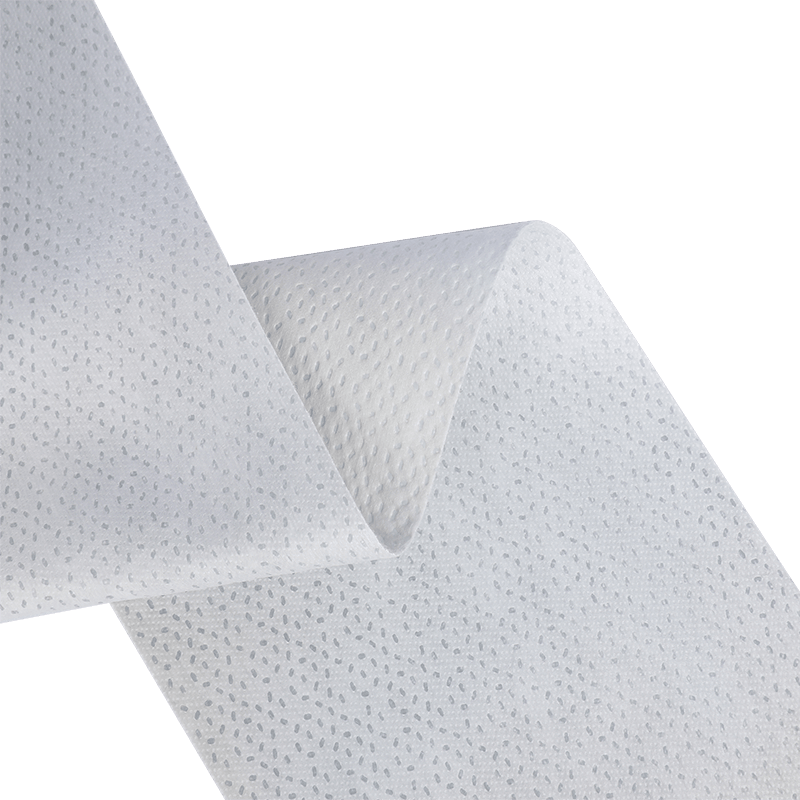