The forming of the fiber web is a key nonwoven manufacturing process. This step helps to create a bonded web and enhances the strength and stability of the fabric. The process also involves stitchbonding the individual fibers of the upper and lower facing layers. After this process, the finished fabric is ready for use. The advantages of this material are numerous. Here is a brief overview of the development of this type of fabric.
Composite nonwoven fabric is formed by bonding together two or more webs. The first and second nonwoven webs are made of polypropylene, while the third nonwoven web is made of nylon. The two webs are bonded together using discrete point bonds. The polyethylene constituent of the multiconstituent filament is fused with the microfibers of the second and third nonwoven fabrics. The result is a high-stretch, stretchy, and breathable fabric.
The composite nonwoven fabric is composed of a supportive layer of self-bonding fibers, preferably synthetic organic fibers, extending in random directions throughout the supporting layer. The fibers are bonded together at their crossing points. The supporting layer is then covered by an upper and lower three-dimensional self-sustaining facing layer. The outer facing layers are stitched together along the width of the fabric by rows of stitches. The row of stitches provides the necessary strength to the fabric in the lengthwise direction.
A composite nonwoven fabric is composed of three layers of fibers bonded together with an inner ply 12. The outer layers are made of two or three ply. The structure of this fabric enables it to provide good strength, flexibility, and drape. This property makes it ideal for medical and protective garments. The polypropylene core provides excellent wicking capacity. This nonwoven fabric is also a great choice for clothing and other products requiring stretch or elasticity.
The composite nonwoven fabric of this invention offers an excellent balance between strength and breathability. Its barrier properties and gamma radiation stability make it an excellent choice for use in medical and industrial applications. The permeability of air in a sample of the composite nonwoven fabric is approximately 35 cfm. The authors of the paper, Partha Sikdar and Shafiqul Islam, a doctor and professor of textile science, describe these benefits of this fabric.
A composite nonwoven fabric comprises three layers of self-bonding fibers. The outer facing layers are bonded to each other at cross-points. The outer facing layers are superimposed on opposite sides of the supporting layer. This forms a multi-layer fabric. The individual fibers of these layers are oriented in the widthwise direction of the fabric. The combination of these properties makes it an ideal choice for a variety of applications.
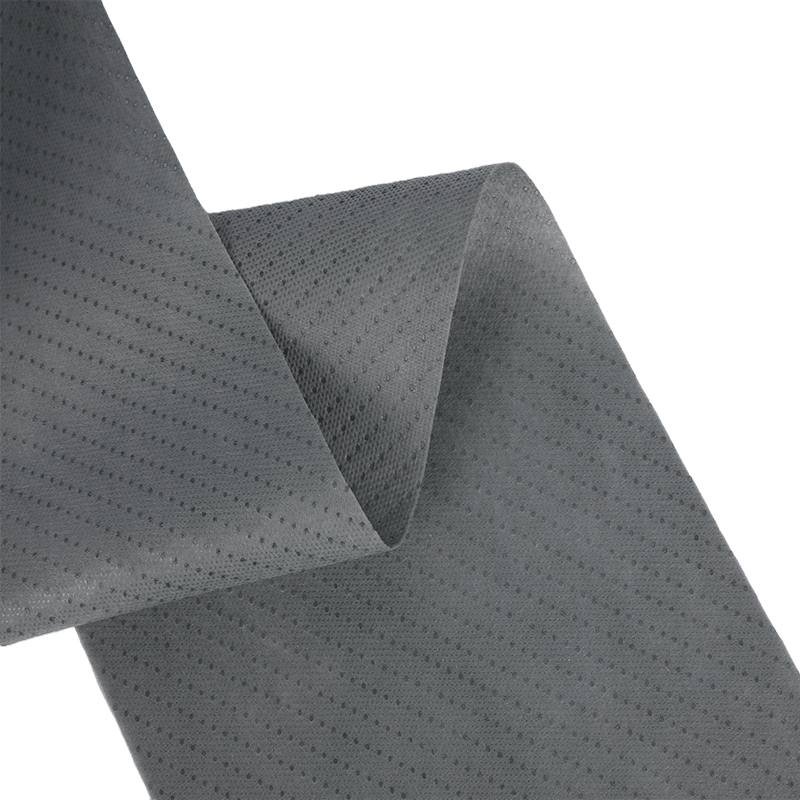